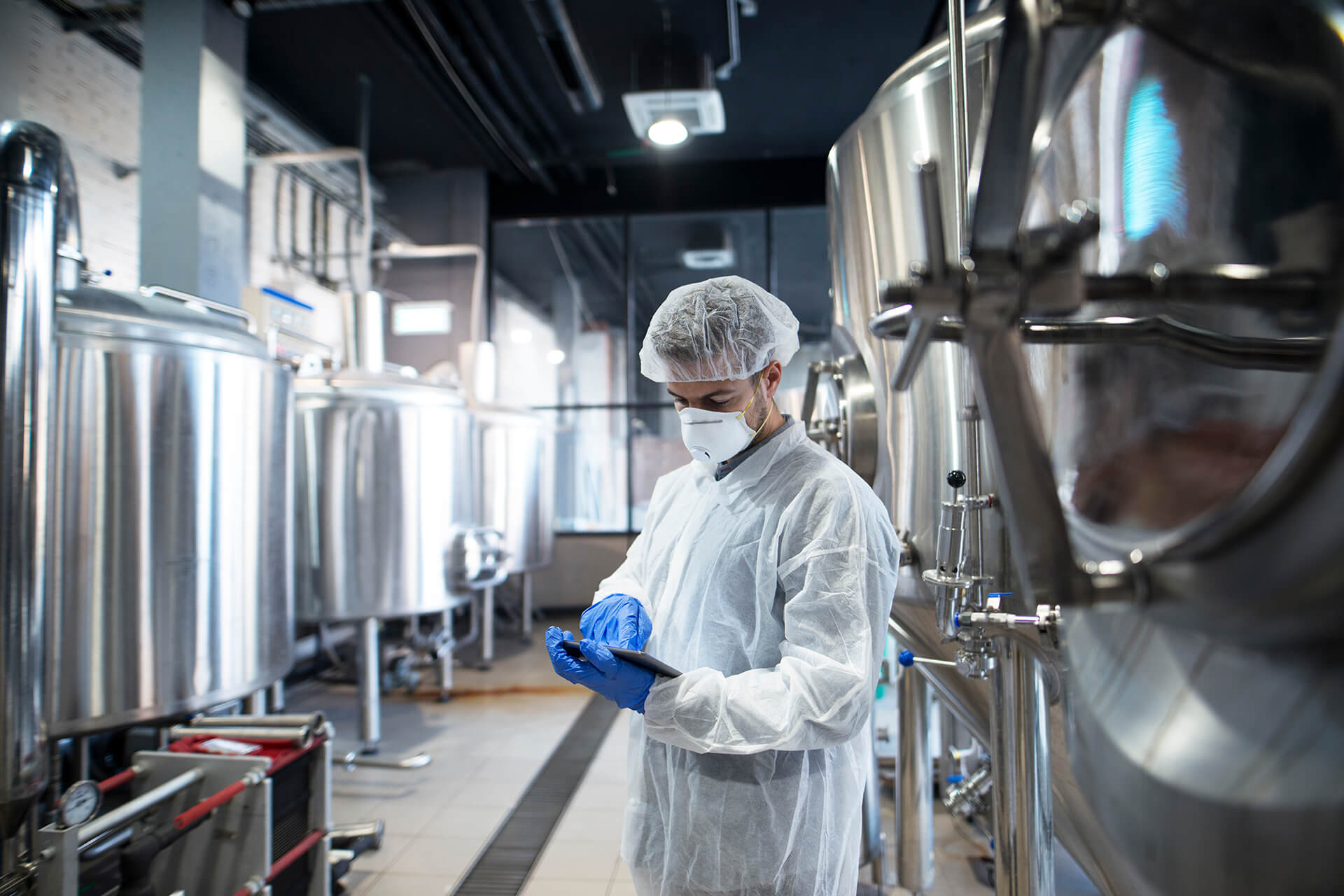
CIP, CIP, HURRAY:
New tools increase efficiency
Breakdowns, bottlenecks, excessive consumption of cleaning agents? We have developed three new tools with which production and cleaning processes in sensitive food manufacturing can be optimally harmonised. This ensures product safety, keeps costs and processes under control and keeps production flowing efficiently.
The staff working at the production facilities deal with complex and closely synchronised processes. The flood of incoming data is correspondingly high. If smartly analysed and clearly presented, they offer huge potential for optimisation throughout the entire production chain. Our team at SCHULZ Infoprod has developed the right tools especially for the food industry. They have focussed on three key areas: production (PR tool), cleaning-in-place processes (CIP tool) and the consumption of energy and media (EM tool). The main aim of the trio for analysis and process optimisation is to uncover bottlenecks and anomalies in the production and cleaning process.
The PR tool is focusing on the complete traceability of the production chain. Mariusz Ziombek, Managing Director of Infoprod, explains: “We map every step. If there is a complaint, we can trace the product back to the raw material. And vice versa: If we receive information about a contaminated raw material, we can intercept affected products in the warehouse.” For the PR tool, our team from Poznan modified and expanded a module of our SCHULZ productionstarĀ® for the food industry.
The modular CIP tool, which is based on Microsoft PowerBI, analyses and optimises the complex cleaning processes. In this way, we support the staff working at the production facilities in choosing the correct cleaning method, for example when allergens need to be removed without leaving any residue. “This is about production safety. In future, we will also use AI for this task,” says Ziombek. The CIP tool also shows when values change over time. “Cleaning can be adapted precisely to the hygiene parameters,” says Ziombek, “while still saving time and resources.”
Our Energy Management, or EM tool for short, is in charge for the evaluation. It is based on the Siemens Energy Manager and displays the energy consumption of single segments. “The combination with the other two tools is interesting. We now have the option of linking data from production, cleaning and consumption. This allows the quantities to be converted to the actual costs per product,” explains Ziombek. He concludes by summarising: “The clearly presented information is easy to read and serves as a basis for optimisation.”
Especially in the food industry, where product safety and strict hygiene standards are required, this smart technology mix of analysis and optimisation tool ensures sustainable and safe manufacturing processes as well as cost-efficient production processes.
We now have the option of linking data from production, cleaning and consumption. This allows the quantities to be converted to the actual costs per product.
Mariusz Ziombek, Managing Director at SCHULZ Infoprod