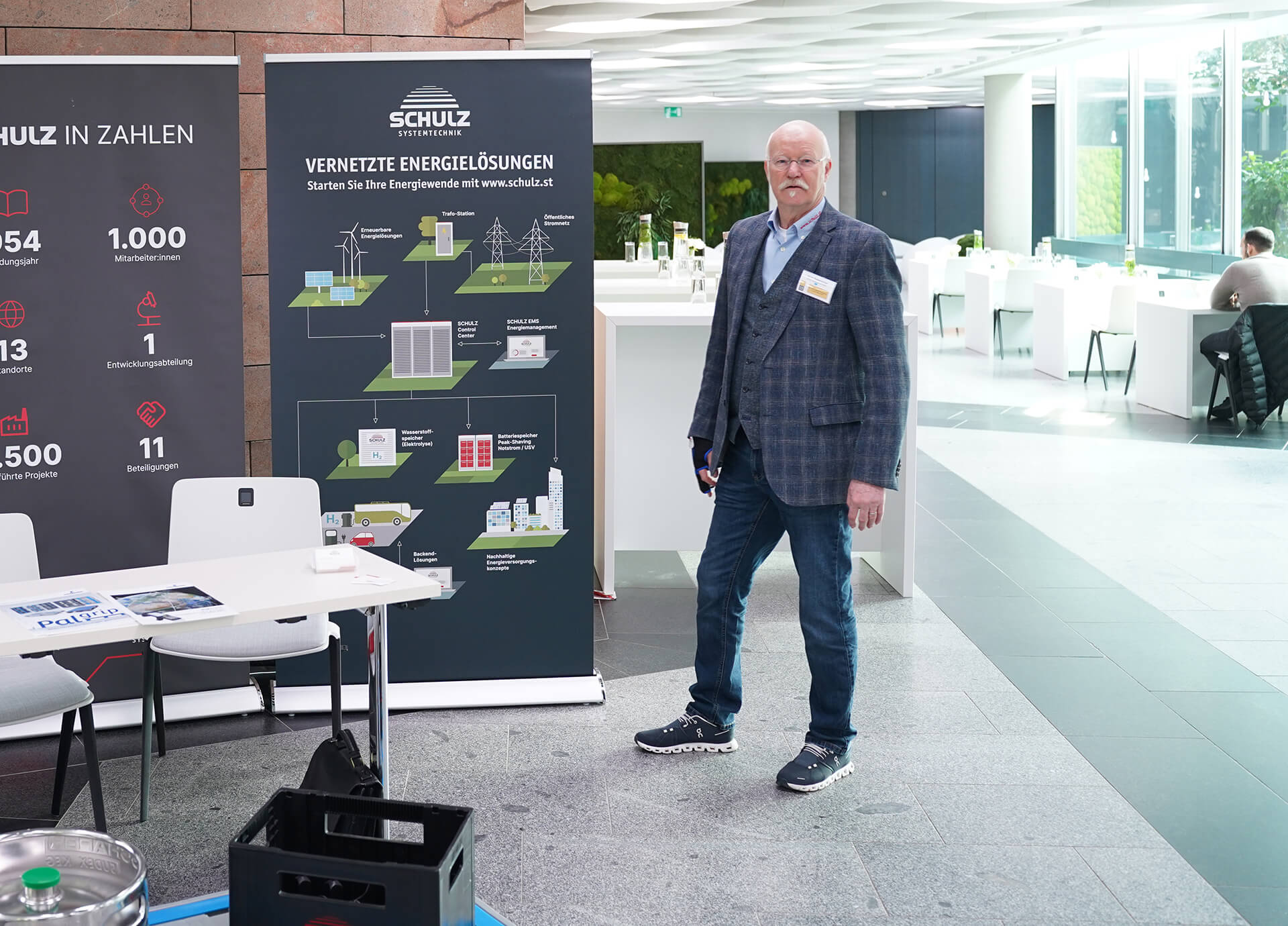
Artificial intelligence
and smart solutions for empties logistics
25. VLB Logistics Congress at the Carlowitz Congress Centre Chemnitz
From 4 to 6 March, the 25th Congress of the European Union was held in Chemnitz. Logistics Congress of the Research and Teaching Centre for Brewing (VLB – Versuchs- und Lehranstalt für Brauerei). With around 170 participants, the congress is the market leader in this segment. The Logistics Expert Committee discussed current trends and issues affecting the brewing industry.
Our colleague Horst Rademacher was also on site. The expert in empties management is a long-standing member of the “Logistik in der Getränkeindustrie” (Logistics in the beverage industry) committee. This year the congress focussed on the use of artificial intelligence in the beverage supply chain, automation solutions for intralogistics, electromobility and alternative fuels. The highlight of the congress was the tour of the Triathlon battery plant in Glachau. The company manufactures high-quality batteries for forklift trucks.
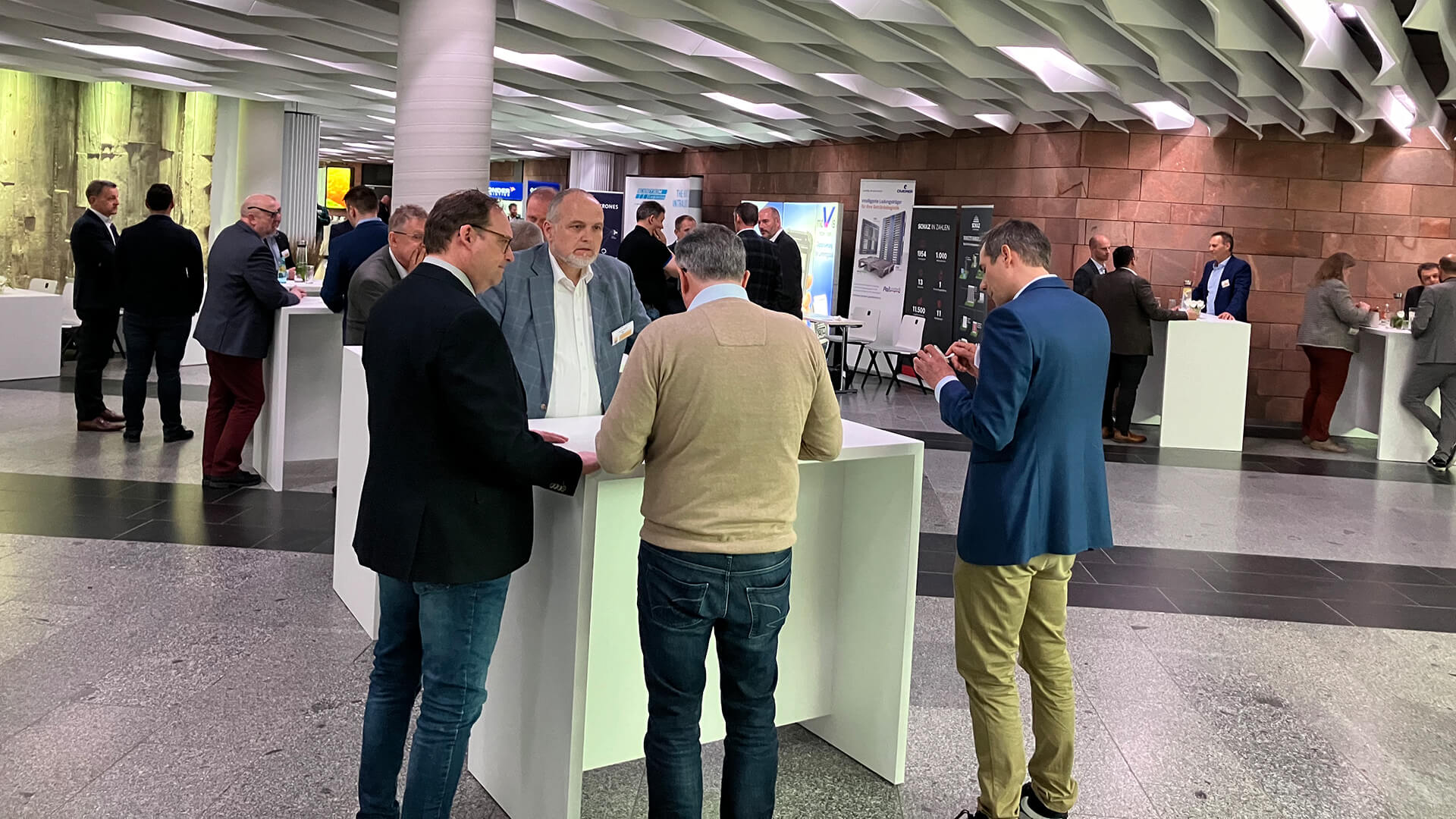
During the conference breaks, the participants met to exchange ideas in the accompanying trade exhibition.
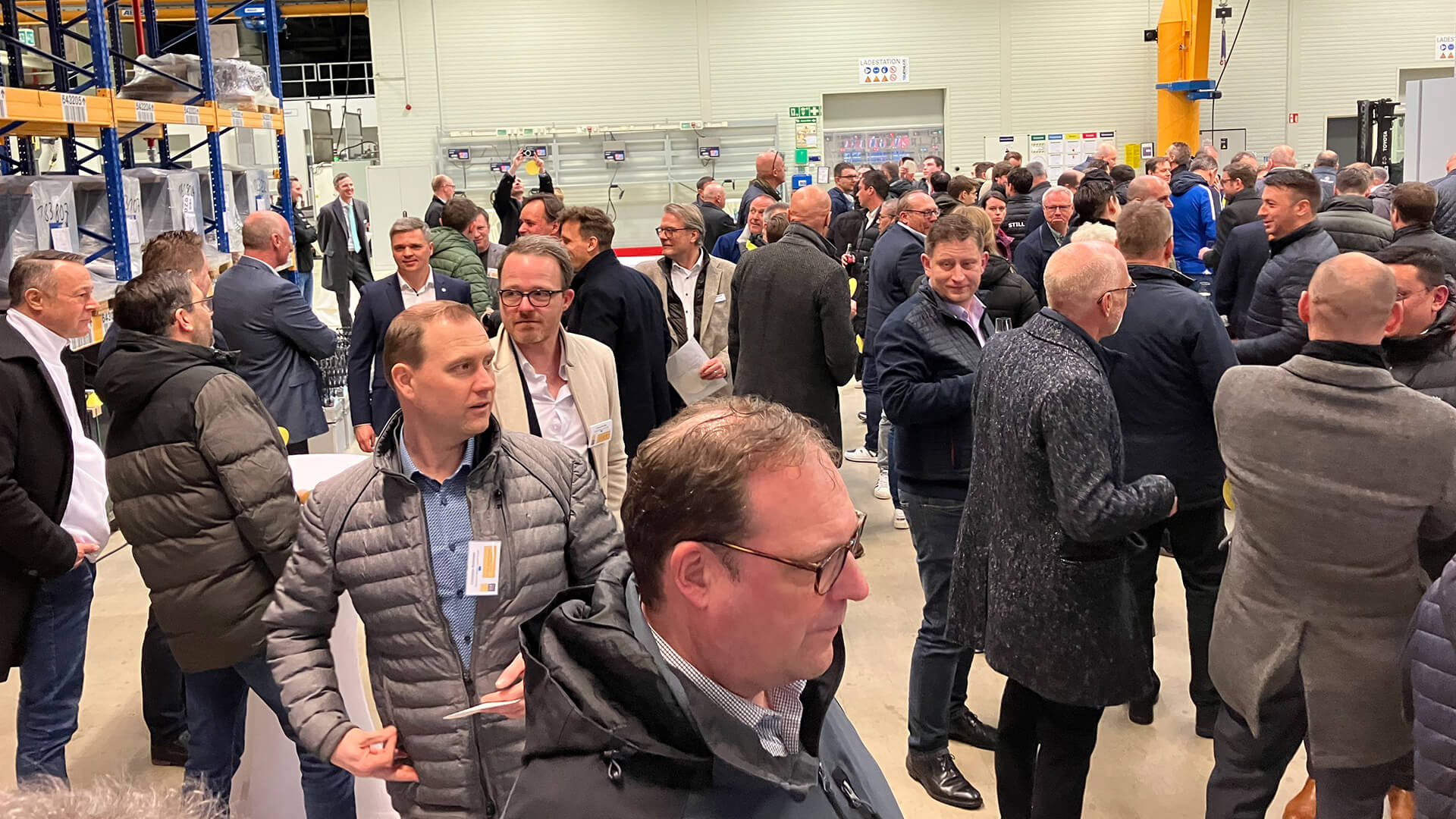
The highlight of the three-day conference was a tour of the Triathlon battery plant in Glachau.
How RFID technology is making logistics processes in the beverage industry more efficient
The three-day congress was rounded off by an accompanying trade exhibition. A perfect platform for exploring best practice examples and ideally suited for informing and talking shop. Together with Frank Bücker from the Craemer Group, a globally recognised specialist in metal forming, plastics processing and toolmaking, Horst Rademacher demonstrated the intelligent use of RFID (radio-frequency identification) technology for beverage logistics at a joint stand. Interested parties were able to view smart crates, drums and pallets directly and find out about our range of services.
Our Kassel site, specialising in identification and sorting systems for the beverage industry, expanded its portfolio last year to include supply chain management and AutoID systems.
“The focus is on equipping beverage crates, beer kegs and event materials with RFID transponders and creating RFID reading stations,” explains our colleague. “In order to optimise our customers’ intralogistics processes, our team in Kassel also carries out feasibility studies and complete process analyses. Based on this, we at SCHULZ then realise our systems, develop the software, test everything extensively and finally integrate the systems at the intended locations at our customers.”
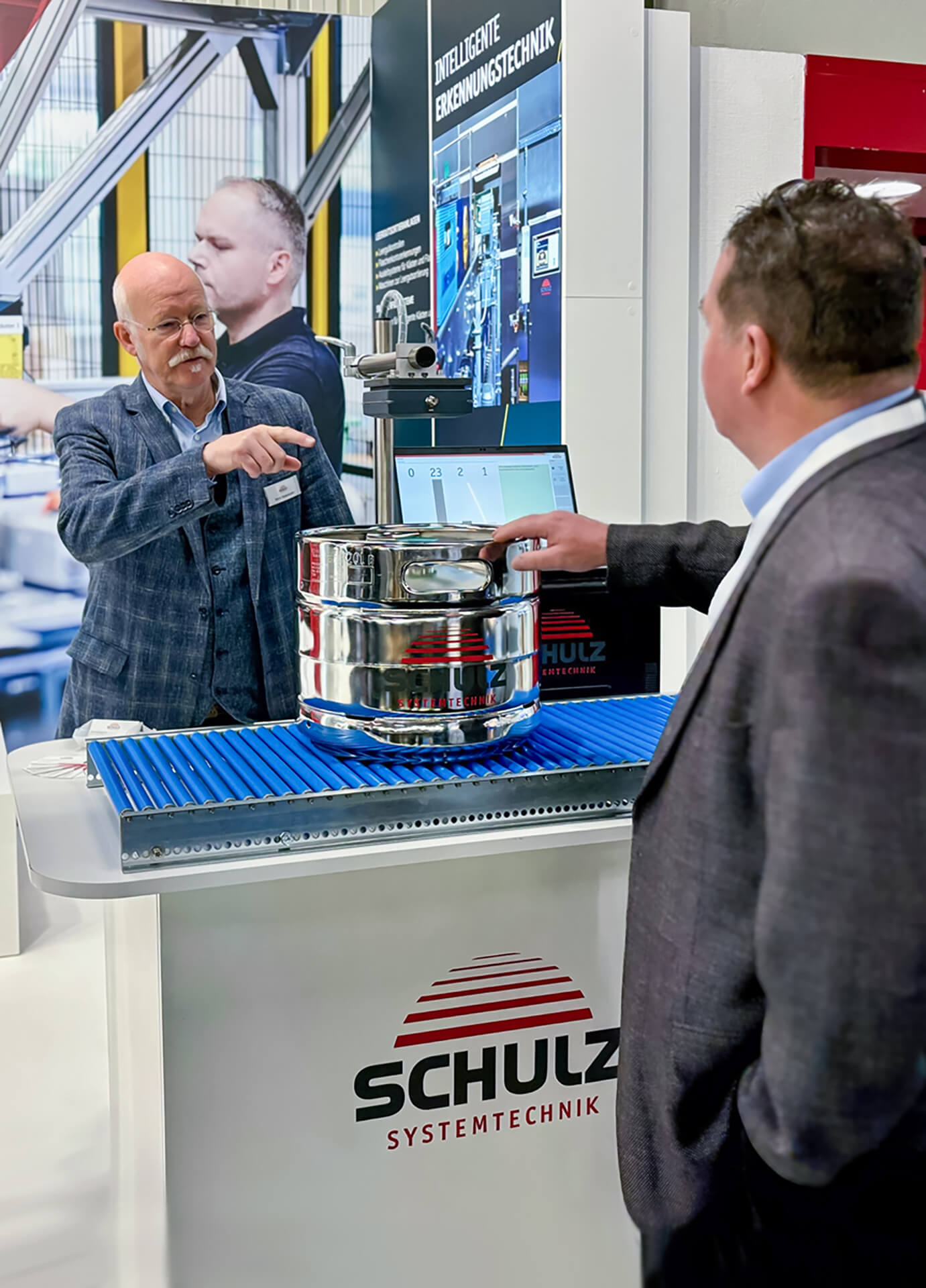
Horst Rademacher demonstrates the use of intelligent RFID technology in beverage kegs.
In order to optimise our customers’ intralogistics processes, our team in Kassel carries out feasibility studies and complete process analyses.
Horst Rademacher, Senior Consultant RFID Technology