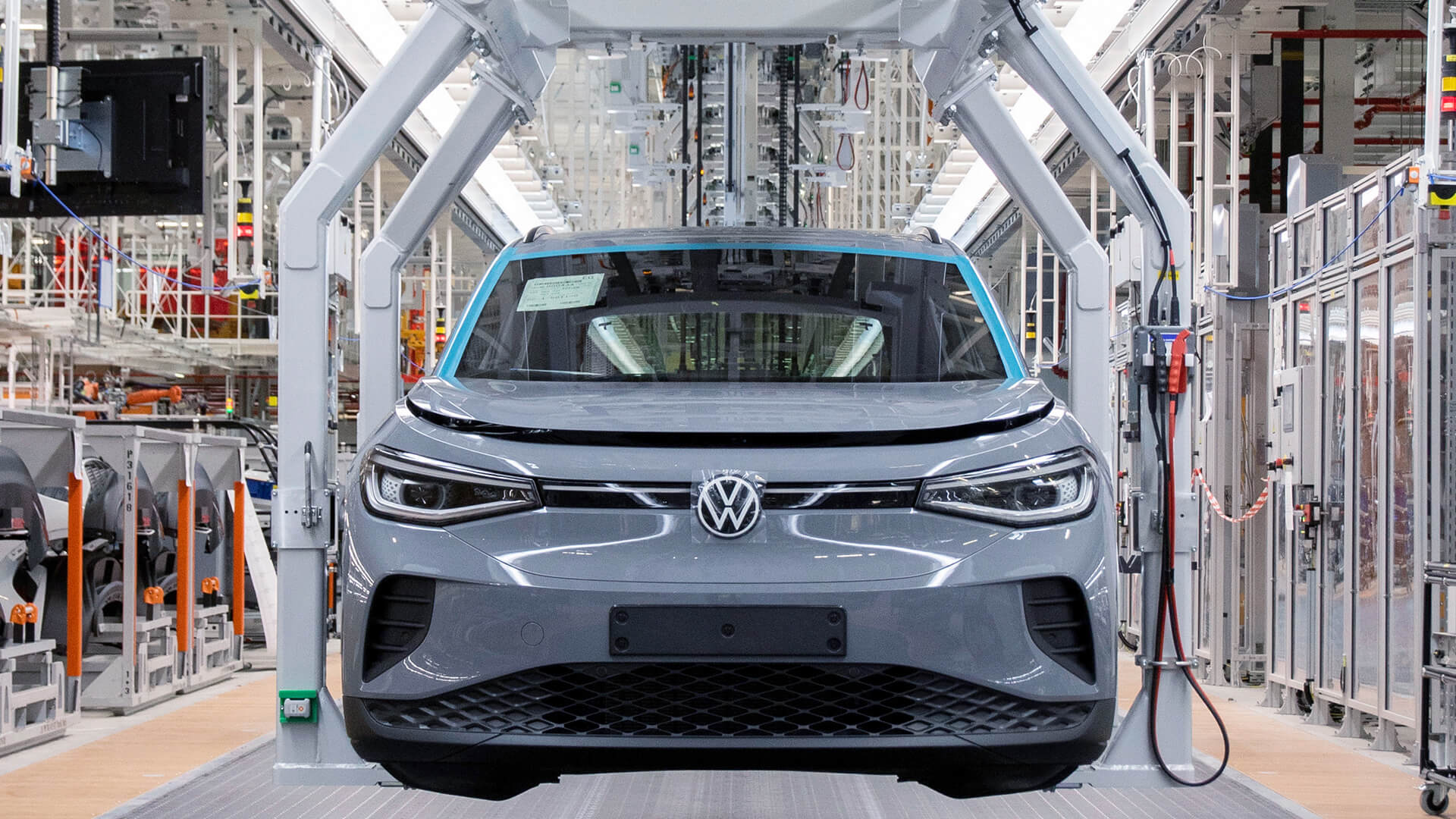
E‑transformation process
at Volkswagen in Emden
While production continues, the company is converting its factory into one of the most modern factories in the automotive industry and a flagship project for electromobility.
Volkswagen in Emden is the largest industrial employer west of Bremen and north of the Ruhr area. Around 163,000 vehicles per year are manufactured on an area of 4.3 million square metres – including the Passat, Arteon and ID.4 models and, since 2023, four-door all-electric Volkswagen Aero. Production of the Passat and Arteon combustion models is to continue until 2024 at the latest, after which Emden will become a purely electric plant.
Since November 2018, the site on the North Sea coast has been preparing for the biggest transformation process in the plant’s history: While production continues, Volkswagen is investing around one billion euros and is converting the plant into one of the most modern factories in the automotive industry and a flagship project for electromobility. Since 2020, a new body shop hall, a bi-colour hall and a new assembly were built, among other things. The Group focuses on environmentally friendly and resource-saving technologies.
Automated piece picking for “just-in-sequence” instead of “just-in-time”
A process that also applies to the production of ID.4. This is where our latest technology for automated piece picking comes into play. The task of the first construction of this type is to place discs of different shapes and colours in a load carrier in the exact sequence in which the corresponding vehicles leave the production line, i.e. a “just-in-sequence” delivery instead of a “just-in-time” delivery. What previously had to be done painstakingly by hand and with an unpredictable error rate is now done precisely and reliably by a specially programmed robot using rail technology.
Digital simulation accurate to the centimetre
Not only does its use save resources, but considerable time and effort could also be saved during planning and installation. “The scenario was digitally simulated to the nearest centimetre in advance in order to be able to place the structure in the tightly calculated space between the existing VW plant technology,” said Daniel Springfeld, our responsible project manager at the Bremen site. “This was a first performance for both us and the customer. All that was needed on site was to fine-tune the robot programming so that production could start swiftly.”
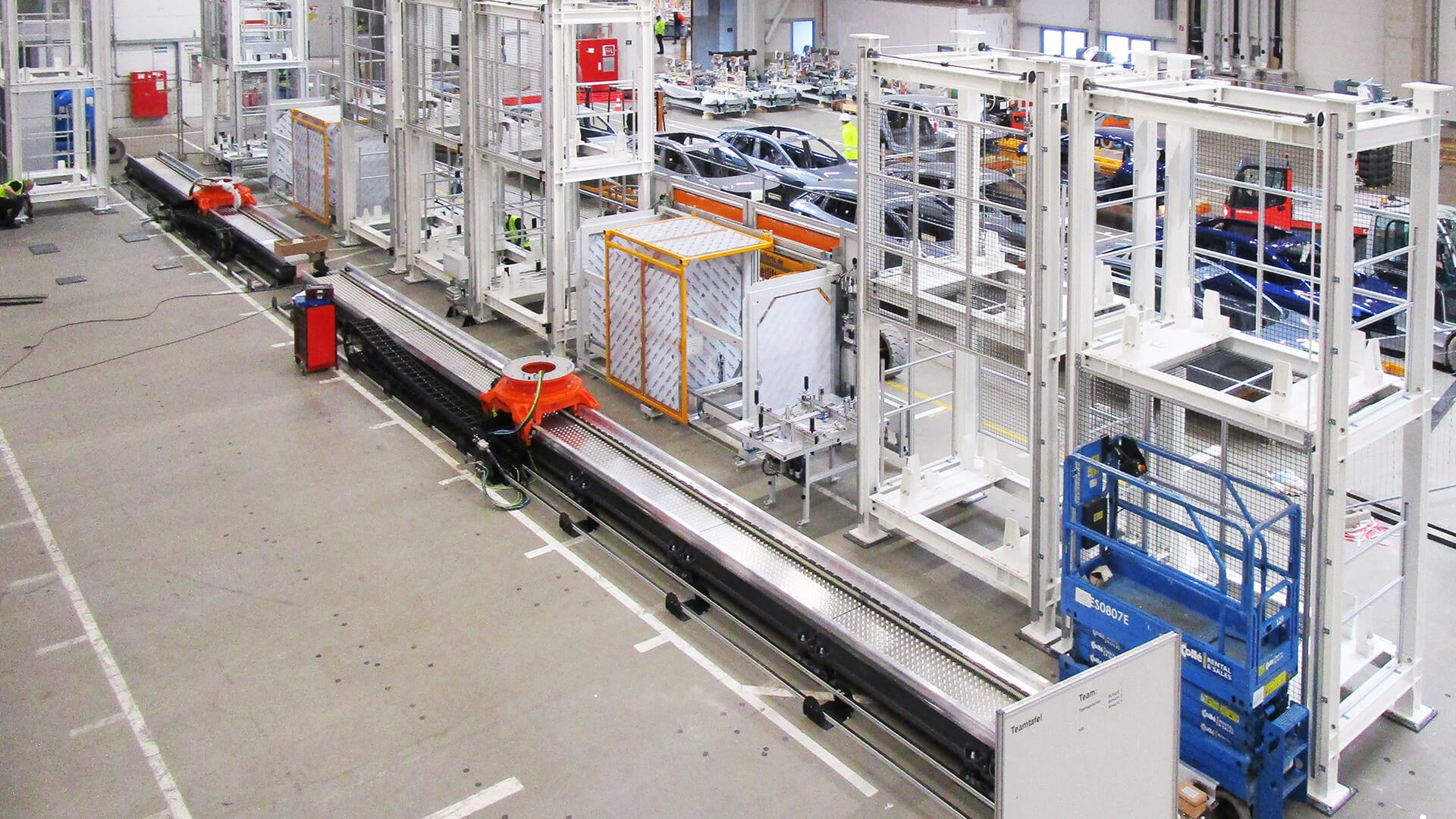
Construction and assembly in the VW hall
The use of components that are as identical as possible for the construction of the windscreen picking system and the installation of the windscreens in the vehicles is a further plus for preserving resources. This means that individual parts can also be recycled in the future, purchased inexpensively or used as multifunctional spare parts.
Mastering challenges with unusual ideas
The fact that the entire project could be completed on time despite the supply bottlenecks during the coronavirus pandemic was not least due to a resourceful idea by Robert Straub, department head in Bremen. “During the testing process of the facility, there was a shortage of automatic circuit breakers that simply could not be obtained. But without automatic circuit breakers, there is no electricity. However, as the technology of these machines has not really changed to this day, I simply installed the ones from my model railway. Despite the delivery difficulties, we were able to keep to the schedule and deliver the system on time.” Sometimes you just have to take unconventional paths to find a solution. VW project manager Holger Raschke also seemed visibly impressed by the creativity of our colleagues. “Some ideas that seemed almost absurd to us at the beginning turned out to be the only feasible and efficient solution in the end,” he added enthusiastically. “You can just feel the experience value. Despite all the challenges, this naturally makes working together fun.”