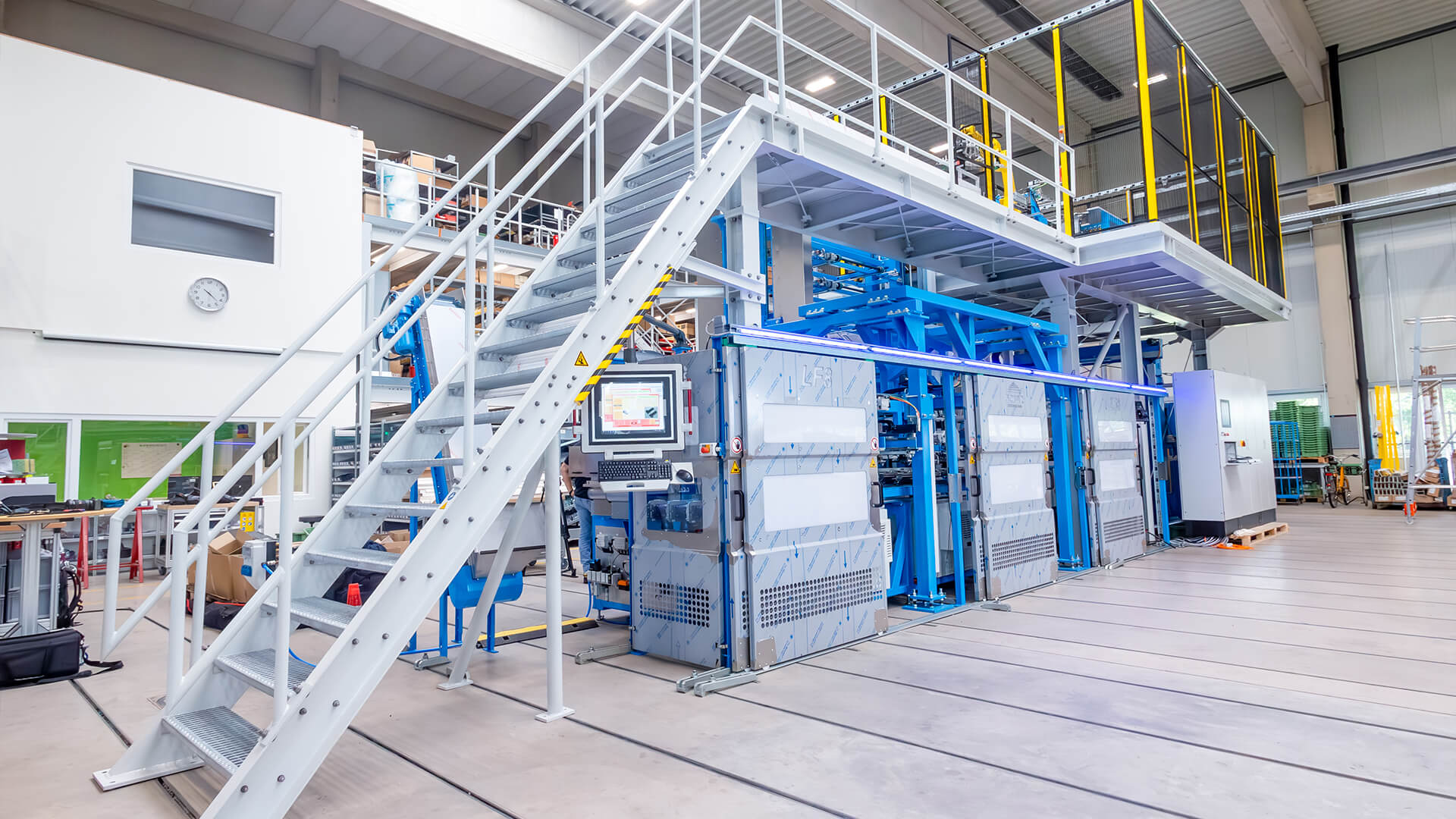
Production process made easier by special machine
Production of cable ducts
AUTOMATIC CARDBOARD FOLDING enhances efficiency in the PACKAGING PROCESS
A new system for the production of cable ducts that can also increase the degree of automation – that was the task that Tehalit (Hager Group), Europe’s leading manufacturer of cable routing systems and inventor of the cable duct, gave our colleagues from the Bremen special machine construction department.
“We built a similar system for Tehalit a few years ago,” explained our colleague Felix Hoffmann, the project manager in charge from Bremen. With an additional machine, the customer can double its production capacity.
“Conceptually, the new special machine is identical to the previous model,” explained our colleague. “Technically, however, it is state-of-the-art and has been partially equipped with other mechanical and electronic components.” It processes the profiles coming out of the extruder, which are shortened to two metres. It equips them fully automatically with four clamps and two couplings so that they can be connected to each other later.
The components are precisely provided using intelligent vision control and feeding technology. The finished profiles are then conveyed to the packaging station. “Automatic cardboard folding ensures greater efficiency at this point,” said Hoffmann. This simplifies the packaging process. Finally, the packaged profiles are labelled and then palletised.
PROVISION OF IMPORTANT PRODUCTION DATA
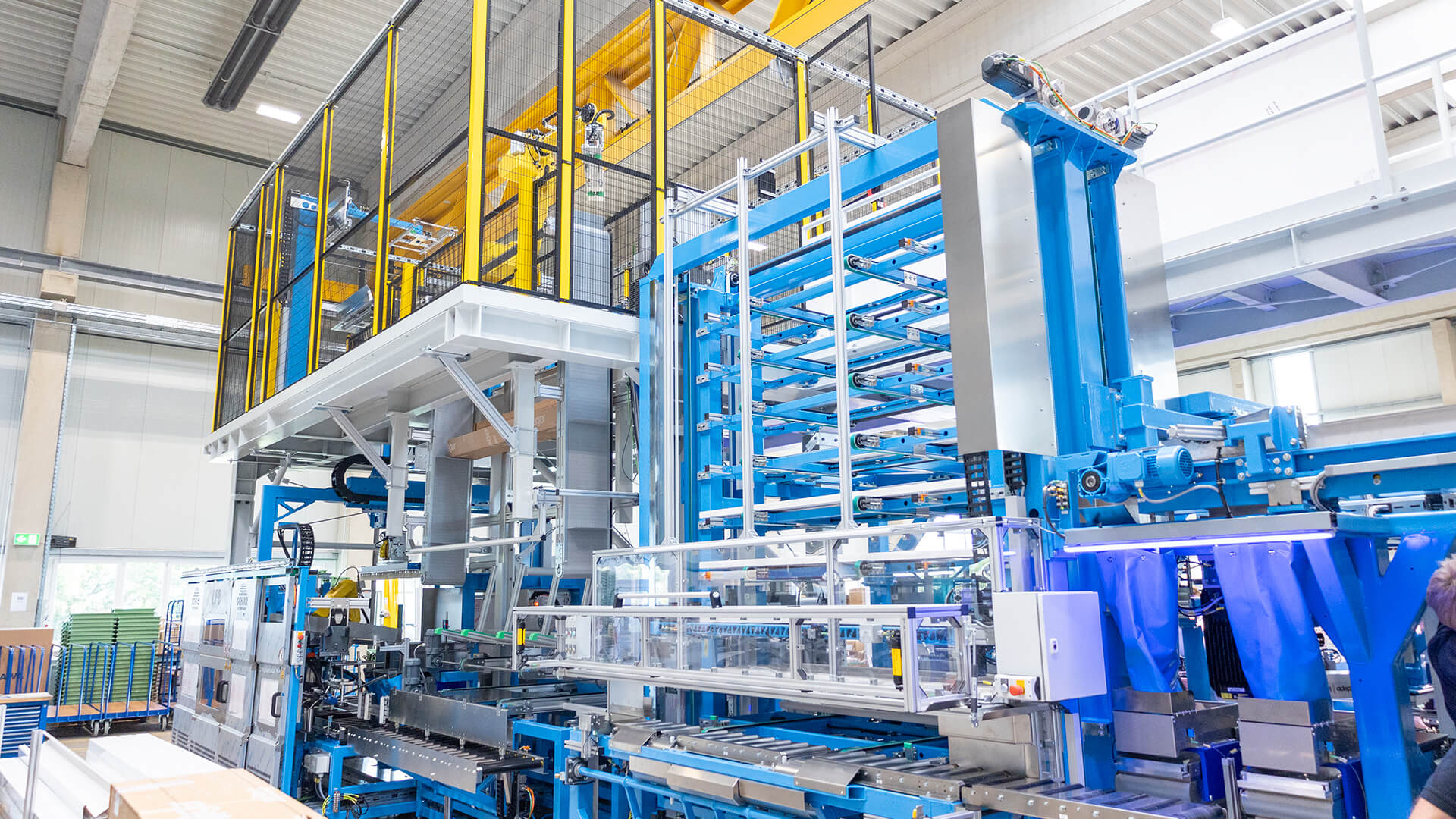
The colossus that assembles, packs, labels and palletises the cable routing channels has two floors and is six metres tall, a good 14 metres long and four metres wide.
However, the new system has even more to offer and provides valuable controlling information. In this way, for example, consumption of electricity and compressed air is automatically recorded and can be converted exactly to the meters produced. Hence, production costs are not only precisely determined, but critical deviations can be immediately identified.
More power and automation, but no more space – that was the requirement. “Not easy,” explained Felix Hoffmann. “Especially with an extremely tight schedule and purchased parts with longer delivery times. Nonetheless, by leveraging our well-coordinated team here in Bremen, we managed to implement everything as planned. The customer was correspondingly satisfied and ordered the next special machine in the same dimensions immediately after commissioning.
More power and automation, but no more space – that was the requirement. As a well-coordinated team, we managed to implement everything as planned.
Felix Hoffmann, Project Manager Special Machinery Construction, SCHULZ Systemtechnik, Bremen